Postmodular Construction: Shaping Tomorrow’s Smart Cities
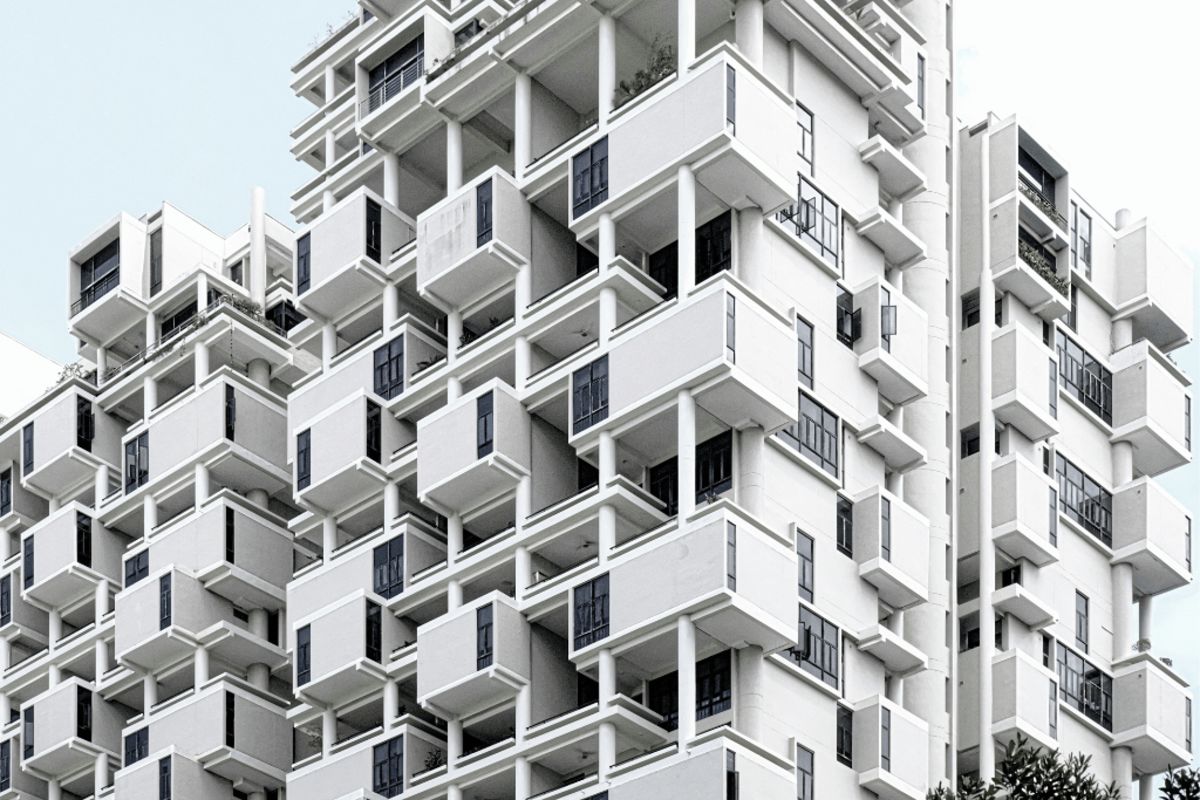
dormakaba Editorial Team
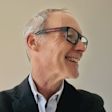
Juan Carlos García Díaz
Juan Carlos is a journalist specializing in Technology and Innovation. He has served as editor-in-chief of the Nintendo Official Magazine and led the creative and content agency Brand Lab within the publishing group Axel Springer in Spain.
Related articles
Urbanization
Cheonggyecheon: How a Reclaimed River Brought Life to Seoul
South Korea's story is one of phenomenal economic growth and rapid urbanization. Following the devastating Korean War between 1950 and 1953, in just a few short decades, Seoul transformed from a war-torn city into a bustling megacity, as South Korea flourished as a global leader in technology and innovation.
Urbanization
Cultural and Political Gentrification: How Urban Spaces Can Survive to It
Urban renewal through gentrification sparks debate—growth for some, displacement and cultural loss for others.
Urbanization
Storm Tanks: The First Line of Defense Against Catastrophic Floods
Climate change brings shorter, heavier rainfalls, boosting flood risks. Storm tanks help by storing and gradually releasing excess water.